This is a very accurate way to calculate how much needs to be milled off the head to get the desired combustion chamber volume.
Use an inexpensive plastic graduated cylinder.
Here is a .032" thick piece of aluminum I cut out to fit the 300 six combustion chamber.
When you mill the head that is the shape of the area being removed, not the whole 4" circle.
Now all I have to do is place the piece in a graduated cylinder of water and see how much water it displaces.
Here is the cylinder with colored water filled to the 70cc mark.
Here is the cylinder with the combustion chamber aluminum piece folded up to fit inside.
The water is now at the 74.5 cc mark.
Aluminum piece is .032" thick for a 4.5cc displacement or .007" per cc.
If you have a flat top piston that is sitting .010" above the block deck at TDC and a head gasket thickness of .050" with a 3.681" bore,
plan for a 57cc combustion chamber for a 9.5 static compression ratio.
Measure the chamber volumes now and do the above procedure to calculate how much needs to be milled to get the correct chamber volume.
Use an inexpensive plastic graduated cylinder.
Here is a .032" thick piece of aluminum I cut out to fit the 300 six combustion chamber.
When you mill the head that is the shape of the area being removed, not the whole 4" circle.
Now all I have to do is place the piece in a graduated cylinder of water and see how much water it displaces.
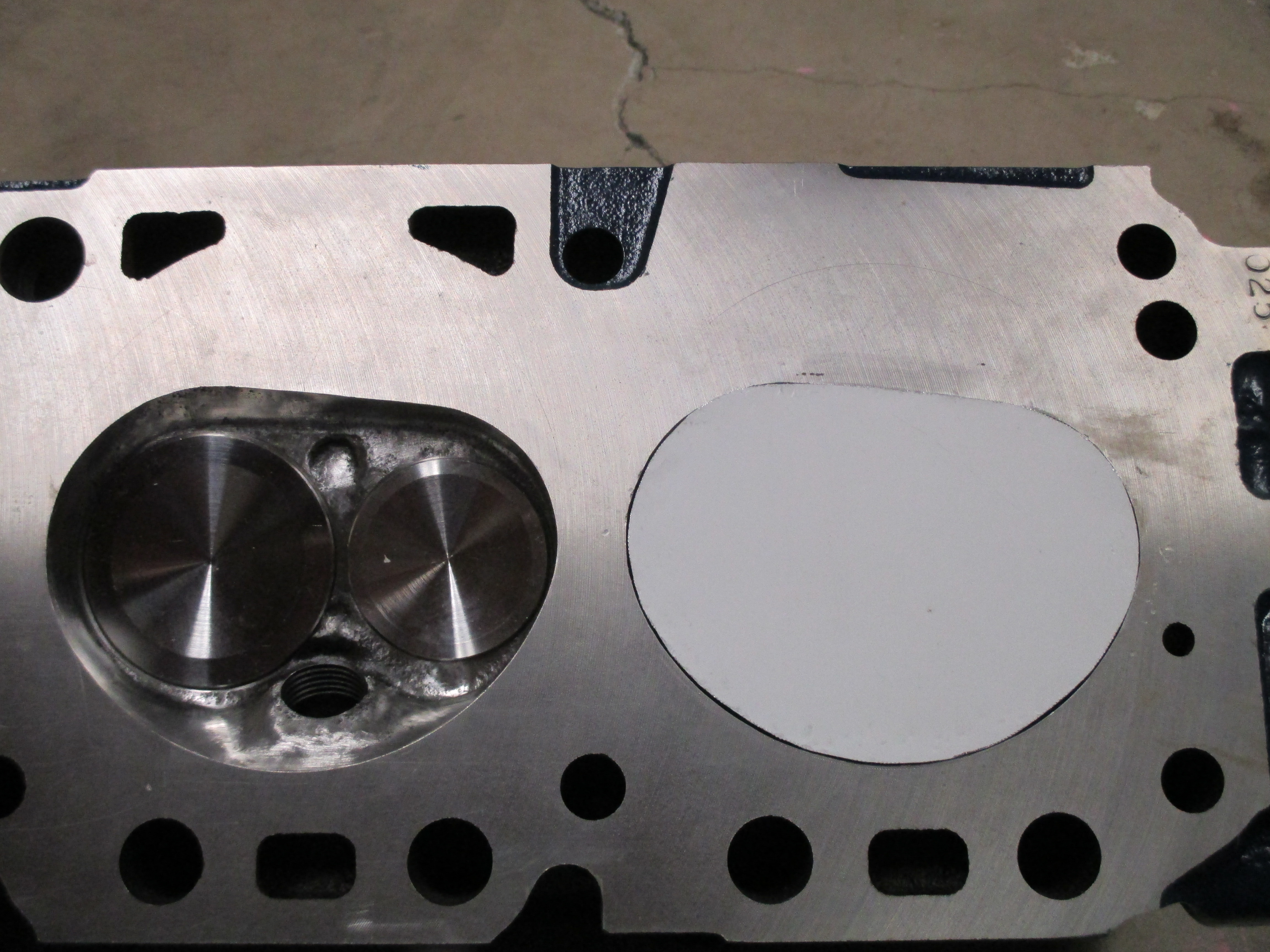
Here is the cylinder with colored water filled to the 70cc mark.
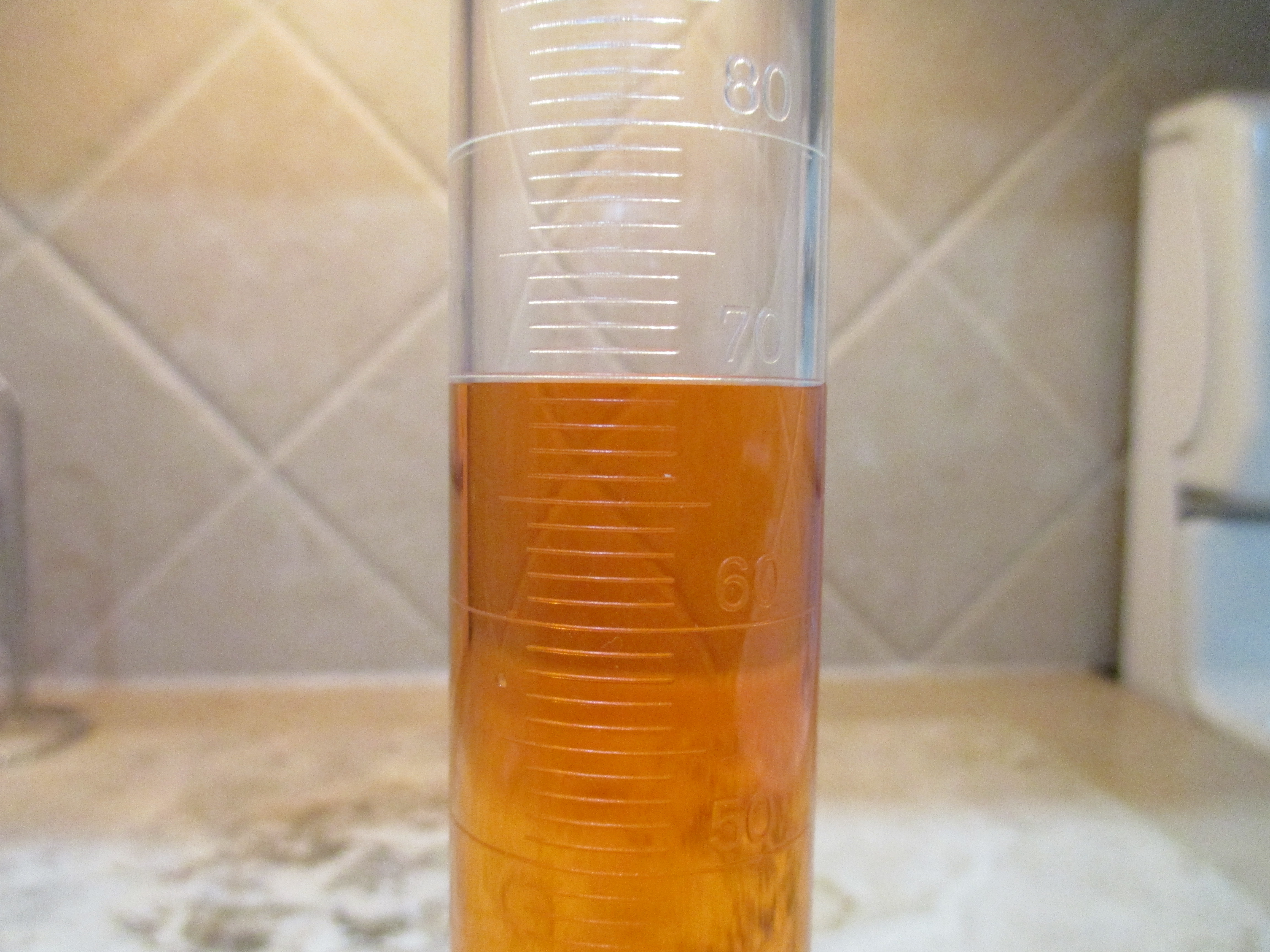
Here is the cylinder with the combustion chamber aluminum piece folded up to fit inside.
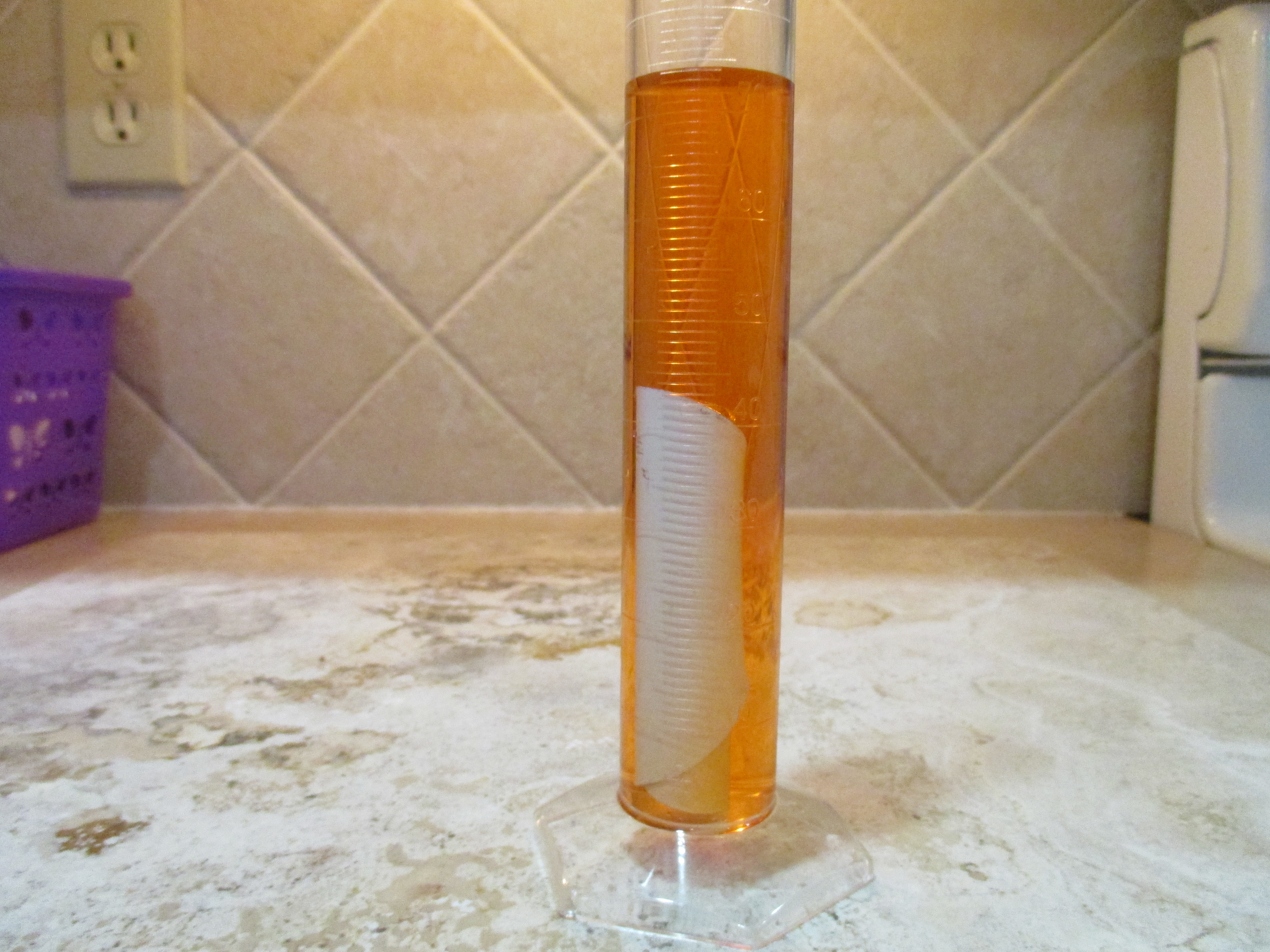
The water is now at the 74.5 cc mark.
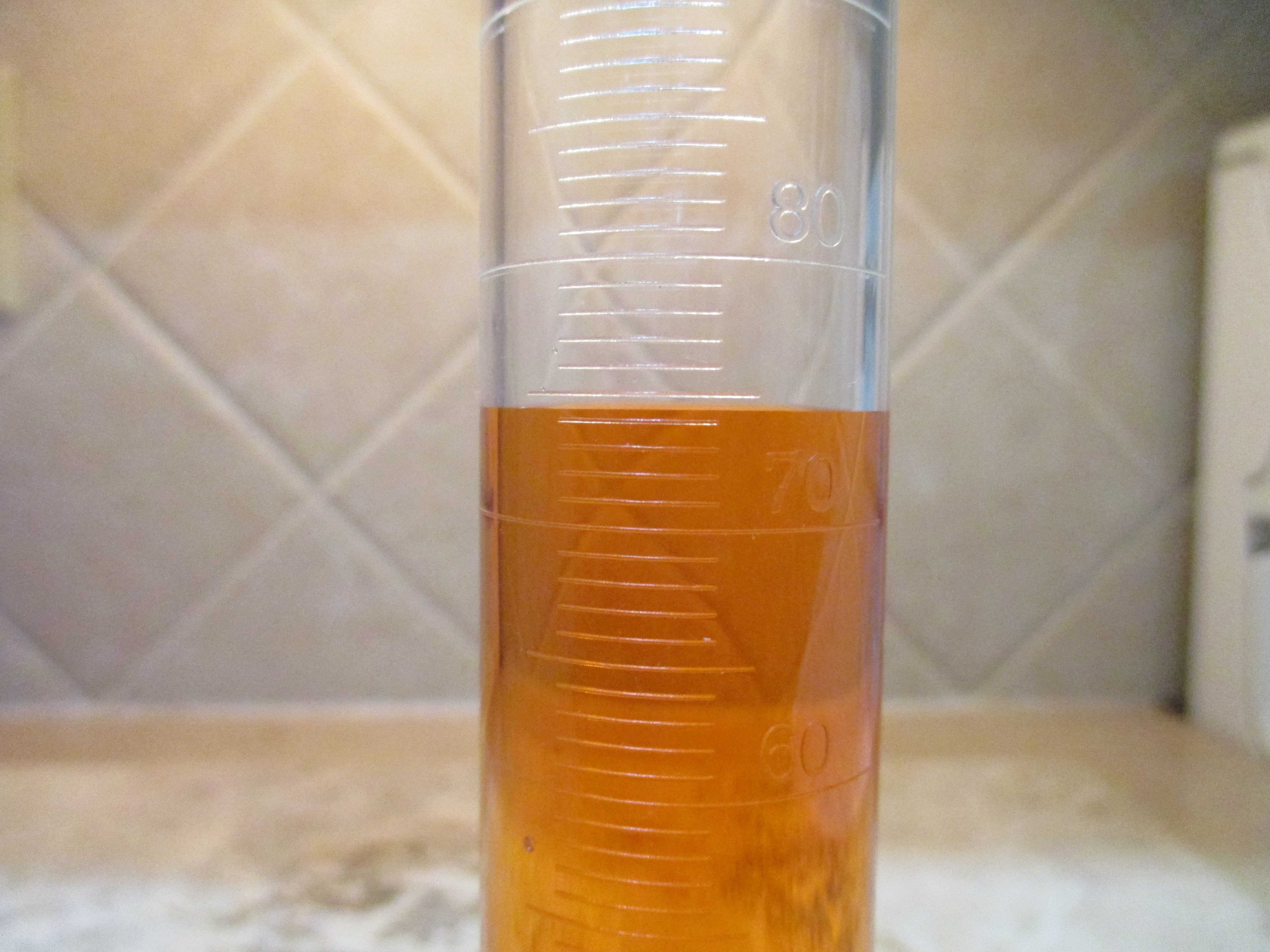
Aluminum piece is .032" thick for a 4.5cc displacement or .007" per cc.
If you have a flat top piston that is sitting .010" above the block deck at TDC and a head gasket thickness of .050" with a 3.681" bore,
plan for a 57cc combustion chamber for a 9.5 static compression ratio.
Measure the chamber volumes now and do the above procedure to calculate how much needs to be milled to get the correct chamber volume.
Last edited: