Baxsie
Well-known member
Spoiler alert: Just get a ford EFI distributor and save your money.
So I did not know about big vs small for sixes, so I ordered a Holley HyperSpark distributor 565-315 thinking it would fit in my 240.
It is pretty obvious that it is not a drop-in replacement:
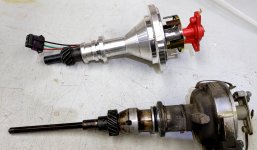
The hole in the block is ~1.4". The Holley 565-315 is ~1.3". Plus the gear is different. And the oil pump drive shaft needs to be longer.
First I turned some sleeves to expand the Holley 565-315 to 1.4":
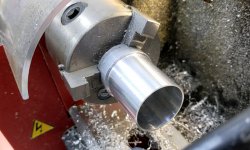
I started with 1.5", 0.125 wall aluminum tubing. Turned the inner diameter to slightly less than 1.3", and turned the outer diameter to 1.4"
Then carefully pressed the sleeves into position using some bearing retainer to make sure they stay put. I left a small gap between the sleeves for the o-ring to live:
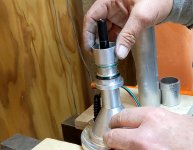
Here are the dimensions of the parts. For a competent machinist, these should be cake to make. It took me a long evening on my cheesey HFT mini-lathe.

The oil pump drive shaft needs to be longer. I cut down a 5/16 long-handle, ball end Allen wrench. I re-used the little circlip from the original rod. As far as I can tell, the circlip is only used to hold the shaft in the distributor during installation.
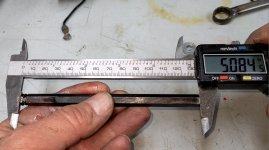
Here is the finished mod (larger Holley o-ring shown, need a 1/16 cross-section o-ring):
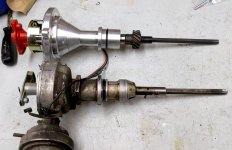
I did have to use some emery cloth to get it to fit into the block. Pressing the sleeves on expanded them slightly.
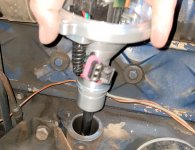
I have a 1 1/4 ID, 1 3/8 OD, 1/16 cross section o-ring on order, but other than that it seems to work:

I did check to make sure that the distributor shaft has some vertical play -- if there is no vertical play that might indicate that the oil pump rod is too long.
Use at your own risk, your mileage may vary, I have not tested it yet, if this mod spews parts into your crankcase and destroys tour $30,000 hot rod engine build that is on you . . . etc.
So I did not know about big vs small for sixes, so I ordered a Holley HyperSpark distributor 565-315 thinking it would fit in my 240.
It is pretty obvious that it is not a drop-in replacement:
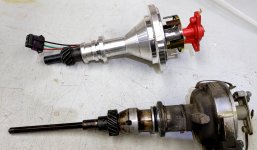
The hole in the block is ~1.4". The Holley 565-315 is ~1.3". Plus the gear is different. And the oil pump drive shaft needs to be longer.
First I turned some sleeves to expand the Holley 565-315 to 1.4":
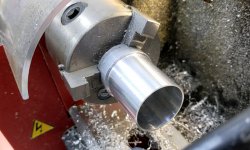
I started with 1.5", 0.125 wall aluminum tubing. Turned the inner diameter to slightly less than 1.3", and turned the outer diameter to 1.4"
Then carefully pressed the sleeves into position using some bearing retainer to make sure they stay put. I left a small gap between the sleeves for the o-ring to live:
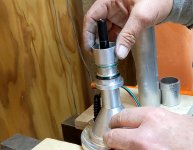
Here are the dimensions of the parts. For a competent machinist, these should be cake to make. It took me a long evening on my cheesey HFT mini-lathe.

The oil pump drive shaft needs to be longer. I cut down a 5/16 long-handle, ball end Allen wrench. I re-used the little circlip from the original rod. As far as I can tell, the circlip is only used to hold the shaft in the distributor during installation.
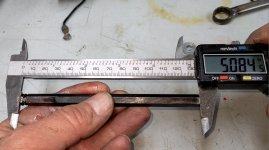
Here is the finished mod (larger Holley o-ring shown, need a 1/16 cross-section o-ring):
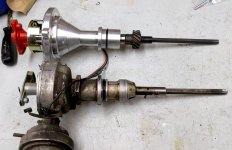
I did have to use some emery cloth to get it to fit into the block. Pressing the sleeves on expanded them slightly.
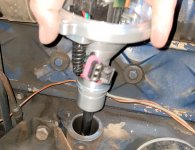
I have a 1 1/4 ID, 1 3/8 OD, 1/16 cross section o-ring on order, but other than that it seems to work:

I did check to make sure that the distributor shaft has some vertical play -- if there is no vertical play that might indicate that the oil pump rod is too long.
Use at your own risk, your mileage may vary, I have not tested it yet, if this mod spews parts into your crankcase and destroys tour $30,000 hot rod engine build that is on you . . . etc.
Last edited: