interested in making carb spacers to my needed specs for 2Bbl log cut and other builds. Looking to 'cast' a few using an epoxy or similar that can withstand the temperatures on top of intake manifold.
suggestions appreciated for any easily available - usable temp' tolerant stuff worth trying to cast.. (self leveling would be nice)
(ref" posts on 2Bbl mod in Small Block forum )
... also - what is estimated temperatures at carb base ?
wrap some tape around something like this and fill ?

,
. 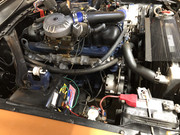
.
. 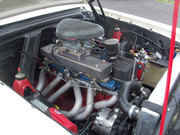
thanks
anecdotally : when I first brought home the '63 wagon, powerwashed the engine and it blew a hole in a freeze plug in the head. Pushed some JB Weld into it with my thumb as a short term fix. It was still not leaking when I pulled the engine a few years later !.
suggestions appreciated for any easily available - usable temp' tolerant stuff worth trying to cast.. (self leveling would be nice)
(ref" posts on 2Bbl mod in Small Block forum )
... also - what is estimated temperatures at carb base ?
wrap some tape around something like this and fill ?

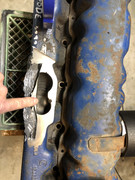
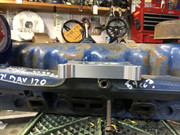
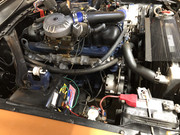
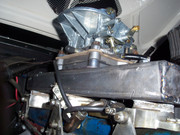
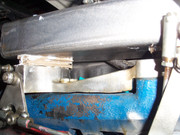
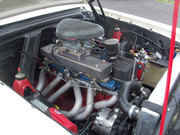
thanks
anecdotally : when I first brought home the '63 wagon, powerwashed the engine and it blew a hole in a freeze plug in the head. Pushed some JB Weld into it with my thumb as a short term fix. It was still not leaking when I pulled the engine a few years later !.
Last edited: